Case Studies
Case Study - Inhouse NEBOSH and IOSH Training

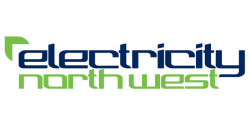
About Electricity NorthWest
They are one of 14 distribution network operators in the UK regulated by Ofgem and the majority of electricity enters our network from the National Grid.
They are responsible for maintaining and upgrading 13,000 km of overhead power lines and more than 44,000 km of underground electricity cables and much more. This covers the diverse communities between the beautiful Lake District landscapes to the bustling city of Manchester and all the wonderful towns and villages located in-between.
The Issue
Due to the nature of the work, the organisation undertakes, the large workforce of Engineers conduct activities which are consider high risk.
Electricity NorthWest wanted to ensure that the engineering teams and their managers had the best understanding of health and safety, and were looking to provide them with leading accredited training courses, to provide them with the health and safety competence needed for their roles.
It was decided that they would outsource the provision of the IOSH Managing Safely and the NEBOSH National Certificate in Construction Health and Safety to an accredited provider.
The solution
Following a proposal that was submitted we meet with the Health of Health and Safety and Training Department to discuss the requirements and the logistics in training such a large number of employees, whilst maintaining their work schedules for service delivery.
The courses were discussed and a plan/ schedule for delivery, over the course of a 12 month period, proposed. This involved a number of trainers delivering training the different courses in accordance with the schedule at the ENWL dedicated training facility in Blackburn.
The training was a success, and we delivered another round of training for the organisation the following year.
Case Study - Covid- Secure procedures
About Dunelm
Dunelm Soft Furnishings is a multichannel retailer with 170 superstores, two high street stores and their website, dunelm.com, featuring extended ranges and delivery convenience (home delivery and reserve & collect) via multi-device functionality and their our own delivery fleet.
In addition to the shops they have 2 large distribution centres in Stoke, which also serves their online operation.
The Issue
Due to the Global Pandemic, and the Government announcement on the lockdown, Dunelm closed all their Stores and their online operations, which included the Distribution centres in Stoke.
However, as the Government guidance was that business could and should remain ‘open’ where safe and possible, the Retailer wanted to use a period of time to ensure their workplaces were as safe and as healthy as possible, before bringing colleagues (who couldn’t work from home) back to work.
In doing so, they were looking for an independent consultant to support them and provide a verification that the measures taken were the necessary ‘reasonably practicable’ controls in line with Health and Safety legislation, current Government advice and Public Health England guidelines.


The solution
A two-stage consultancy project was proposed.
Firstly, a site visit prior to colleagues returning, to review the measures implemented and, secondly, a follow up visit to determine the efficacy of the measures after colleagues had returned.
We visited site and conducted an extensive inspection (walk through) of the premises, starting in the Car Park, from when colleagues first arrive, to determine the areas of risk (from virus infection and spread) to colleagues during normal operations. This was undertaken with the Health & Safety Team, Site Management, and other site personnel.
During the visit measures were reviewed (and challenged in some instances) and a report produced including some further actions that had been discussed during the visit.
After an extensive programme of implementing measures, colleagues returned to work after 8 days of closure.
A further follow-up visit was undertaken to review the measures and determine how colleagues were operating under the new regime of controls. A further report was provided to the client on the conclusion of the review.
It was very encouraging to see how Dunelm had implemented, communicated and managed colleagues return to work to ensure they remained safe and healthy as possible.
Case Study - Health and Safety Management System


About Gresham Office Furniture
Gresham Office Furniture Ltd is one of the largest independent designers and manufacturers of workspace furniture in the UK.
They employ more than 250 people based from a 200,000 sq ft office and factory space in Greater Manchester.
As well as clients across the UK, they serve markets in the Middle East via showrooms in Abu Dhabi and Oman.
The Issue
We were asked to carry out an audit on their existing health and safety management system to assess their compliance with relevant legislation and industry best practice.
The Company were aware that their systems had lapsed over recent years and that despite the company growth, health and safety had not kept up the development of their management systems.
The Company were looking to employ the services of external health & safety professionals who would be able to improve their systems and ensure that it was effective and manageable.
We found that the Company were managing risks at ‘shop floor’ level to a satisfactory level however there was no formal management system in place; they had no health and safety policy on which to build, risk assessments were either missing or out of date and training had not been refreshed for some time.
The solution
We started with the foundations at this Company by developing a new health & safety policy, from which the rest of the management system has developed. A full risk assessment inventory was completed and we spent 18 months developing a series of suitable and sufficient risk assessments which cover all the company activities from furniture manufacture through to delivery of their bespoke furniture and everything in between. In addition to this, safe systems of work and a fully operations permit to work system has been developed and implemented.
We have developed a training programme to suit all levels of employee, from Directors down to shop floor staff; included accredited qualifications/courses such as NEBOSH National General Certificate (for their now HSQE Manager) IOSH Safety for Senior Executives, Managing Safely through to bespoke courses in health and safety awareness.
We spent time working very closely alongside the HSQE Manager and other personnel to transform the organisation into one with a positive health and safety culture, which is supported by an effective and formal management system which is managed internally with continuous support from us.
Where they are now?
The company have been accredited to ISO 45001 and continue to work with us in maintaining their positive health and safety culture.